When it comes to business, there’s a lot of moving parts. Maybe you’re an entrepreneur who’s just trying to get started, and you’re looking at your first ever equipment purchase. Or maybe you’re an established small business owner who is trying to figure out how to make the most of an old and outdated piece of machinery.
Either way, it can be tough to know what’s going on in the world of equipment management. That’s why we’ve put together this guide: to help you navigate the world of pre-start checklists for equipment by breaking down frequently asked questions.
What is a pre-start?
A pre-start is a list of all the things you need to do before you can start operating your equipment. It’s usually set up as a checklist so that you can go through each item one by one and make sure everything is in good working order before you get started. They are used in almost every industry but are very common tool used in construction, mining, and earthworks.
What is the benefit of a pre-start?
The benefit of having a pre-start checklist is that it can help prevent and manage problems with equipment. For example, if you don’t have the right tools for the job, you might end up ruining something expensive or even rising the safety of yourself and everyone around you. By checking off the items ahead of time, you’ll know if something needs to be purchased beforehand or if there’s some other problem that needs to be resolved before you begin using the equipment. A pre-start also helps to ensure that all equipment is in compliance with industry standards and to confirm that necessary permits and approvals are in place. In such a scenario you can avoid fines or any unnecessary closures.
What should be on my pre-start?
The exact items on your pre-start checklists will vary depending on what kind of machinery or equipment you have, but there are some common things that should be included. For example, if you have any electrical items, it’s important to check the circuit breakers or fuses to make sure they’re operational and in good working order. You may also want to check if any filters need changing or replacing, or if there are any other maintenance tasks that need doing before starting up again after being turned off for an extended period of time (for example, when leaving machines over winter).
How often should a pre-start be performed?
Once you have created your pre-start checklist, it is important to establish a regular schedule for performing the checks. Depending on the type of business and the risks involved, checks may need to be done daily, weekly, monthly or even before each shift. For most businesses, checking at the beginning of each workday is sufficient but if you have complex machinery, it will likely have to be done before you turn on the machine.
How to use a pre-start checklist to improve productivity?
A pre-start checklist can also help improve productivity by ensuring that all necessary tasks are completed before work begins. This can save time and frustration later on, as workers will not have to stop in the middle of their work to complete forgotten tasks. Additionally, a well-designed pre-start checklist can help workers plan their work more efficiently, leading to greater overall productivity.
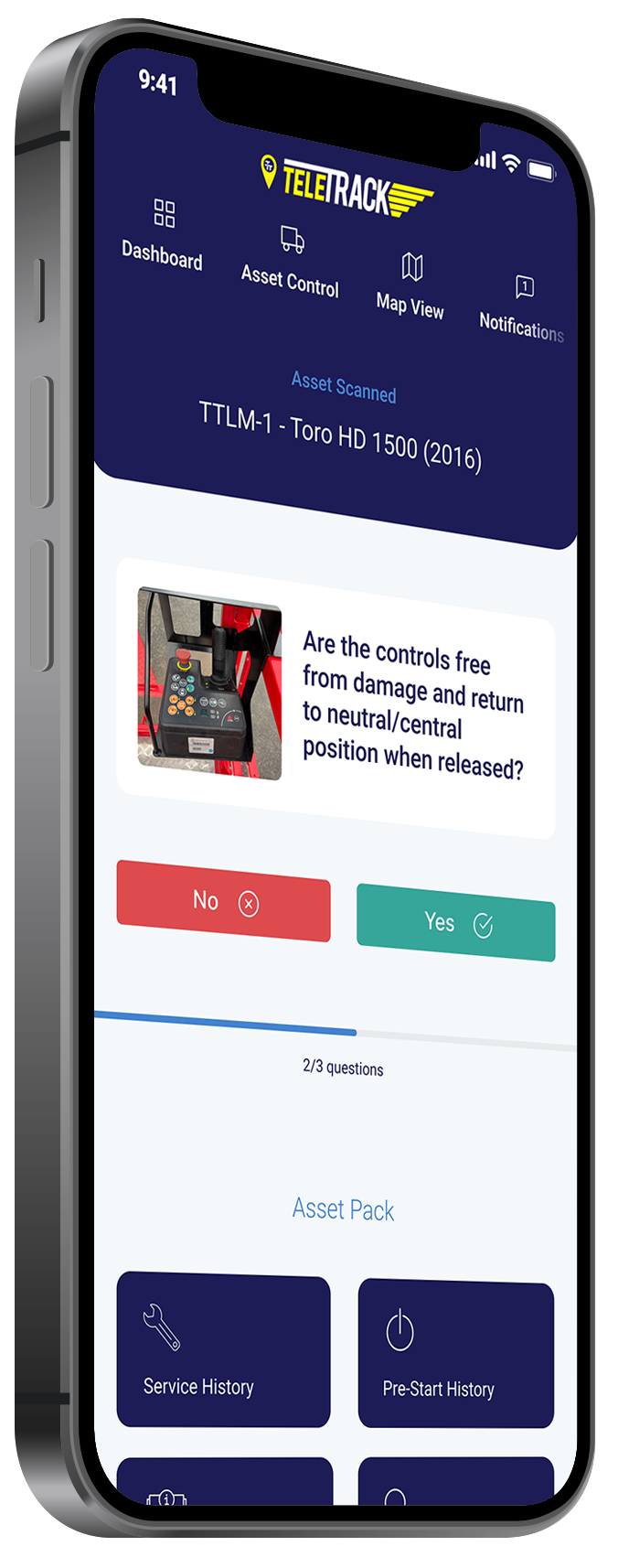
Conclusion
A pre-start checklist is an important tool that can be used to avoid accidents and improve productivity. By including items such as a safety check, equipment check, and task list, a pre-start checklist provides a comprehensive overview of the work to be done. By performing a pre-start checklist on a regular basis, you can ensure that all tasks are completed safely and efficiently.
Learn more about our Pre-Start features and functionality here.